
Design a running (gate) system with risers that ensure a continuous flow of molten metal.You can prevent shrinkage casting defects by improving the overall casting structure: Factor a shrinkage allowance into the pattern design before casting. You should expect some shrinkage during solidification. This is because the density of a casting alloy in the molten state is lower than that in the solid state. Prevent shrinkage cavities by improving casting structureĪlloys always shrink when changing from molten to solid. Macro shrinkage can be viewed with the naked eye, but micro shrinkage cannot.Ĭlosed shrinkage defects usually appear at the top of hot spots, or isolated pools of hot liquid. Closed shrinkage defectsĪlso known as shrinkage porosity, closed shrinkage defects form within the casting. Caved surfaces are shallow, open shrinkage defects that form across the surface of the casting. Pipes are open shrinkage defects that form at the surface and burrow into the casting. Air compensated as the shrinkage cavity forms. Shrinkage can result in two types of casting defects. Large shrinkage cavities can undermine the integrity of the casting and may cause it to eventually break under stress. Cavities might also be paired with dendritic fractures or cracks. Shrinkage porosity appears with angular edges, compared to the round surfaces of gas porosity. Shrinkage occurs because metals are less dense as a liquid than a solid.Ī shrinkage cavity is a depression in a casting which occurs during the solidification process. Increase rate of solidification by reducing metal temperature during casting.Dry out molds and cores before use and store dry.Allow air and gas to escape from the mold cavity

Increase permeability of mold and cores.Increase gas permeability of sand: coarser sands have a higher permeability.Incorporate good fluxing and melting practices: melt metal in a vacuum, in an environment of low-solubility gases or under a flux that prevents contact with the air.Inadequate gas permeability of molding sand.Excessive moisture content of molding sand.Scars are shallow blows that appear on a flat surface, while blisters are scars covered with a thin layer of metal. There are several causes of cavity defects. These blowholes appear on the surface of the cast and are easier to detect than subsurface blowholes. Subsurface blowholes can be difficult to detect before machining, requiring harmonic, ultrasonic, magnetic or x-ray analysis. Subsurface blowholeīlowholes, or simply blows, are larger cavities than pinholes.Ī subsurface blowhole appears on the inside of a cast and usually isn’t visible until after machining. They are always visible to the naked eye and don’t require equipment to identify. They usually appear in large numbers together, either at the surface or just below the surface of the casting. Pinholes, also sometimes referred to as porosities, are very tiny holes (about 2 mm) usually found in the cope (upper) part of the mold, in poorly vented pockets. There are three types of casting defects related to gas porosity: 1. These bubbles appear on a casting as rounded, circular cavities or holes. When the casting cools and solidifies, bubbles form because the solid form of the metal cannot hold as much gas as the liquid form. Gas porosity occurs when the metal traps gas (most often nitrogen, oxygen or hydrogen) during casting. Read on or click the links below to jump to the section for each of these types of casting defects. Only then can you prevent casting defects and avoid sending defective products to your customers.

The key to preventing product defects in your casted products is to set clear expectations and tolerances for quality issues with your supplier ( related: How Experienced Importers Limit Product Defects in 3 Stages ).īut before you can do that, you need to have a clear understanding of the different types of casting defects and their causes.

Skills of the operator, quality management and equipment can all affect the final quality of the casting. The technical level of each process varies greatly. What happened? How could you have prevented this from happening?įoundry production is a complex multi-step process. Your cast iron metal pan leaves the factory with pinholes, leading to a slew of complaints from your customers.
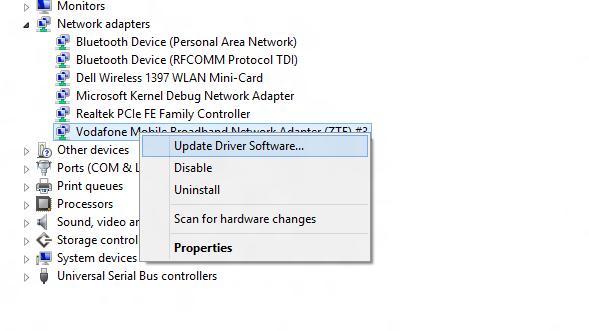
Read on for causes and prevention of the top casting defects. Are your products suffering from casting defects? The good news is they're entirely preventable.
